Na construção e na indústria, as operações de soldagem são comuns, permitindo a montagem de estruturas duráveis e mecanismos de diferentes graus de complexidade. No estágio de monitoramento da emenda resultante, nem sempre é possível avaliar a confiabilidade do conjunto conectado dentro da estrutura. Para isso, são utilizados métodos não destrutivos de teste de juntas soldadas. O método radiográfico de análise é um dos mais comuns neste nicho.
O princípio da operação do controle radiográfico
O método é baseado no uso de radiação radioativa, que permite analisar a estrutura interna do material sem intrusão física com deformação. Para isso, raios-x e raios gama que passam pelo produto são usados. Como resultado, o operador recebe um mapa de defeitos estruturais registrados em um filme magnetográfico. A radiação permite formar uma imagem com contornos ocultos da estrutura, cuja decodificação é executada em um desenvolvedor especial no processo de processamento de fotos. Em cada caso, os parâmetros para realizar a inspeção radiográfica das juntas soldadas de acordo com GOST 23055-78 podem variar - até 6 de diâmetro e de 1 a 10 mm de comprimento em relação aos poros e falta de penetração. Se o comprimento do radiograma geral for inferior a 100 mm, a área total de defeitos diminuirá proporcionalmente ao comprimento do cartão. A profundidade de penetração dos raios X é determinada pelos parâmetros da peça.

A tecnologia de controle radiográfico é freqüentemente usada em conjunto com o método ultrassônico de análise da estrutura dos materiais. Tal combinação geralmente ocorre em situações em que o uso de ultrassom não é tecnologicamente possível. Além disso, a varredura de feixe fornece mais informações sobre os dados geométricos de lesões de corrosão e corrosão. Diferenças na inspeção ultra-sônica e radiográfica das juntas soldadas estão relacionadas à eficácia do estudo de defeitos com diferentes formatos. No primeiro caso, é mais provável que a detecção automática de falhas ultrassônicas se concentre em trabalhar com falhas no plano na forma de imperfeições e rachaduras. Por sua vez, a radiografia fornece alta precisão na análise de defeitos de volume.
Nomeação de controle radiográfico
Este método de controle é utilizado para avaliar a qualidade de uma junta soldada de metais e ligas cuja espessura varia de 1 a 40 cm, sendo os defeitos determinados principalmente na estrutura interna dos produtos nas condições de ausência local de inclusões estrangeiras, poros tecnológicos e solda. Além disso, de acordo com GOST, juntas soldadas no momento da inspeção devem ser livres de escória, respingos de fusão, escala e outras impurezas deixadas durante o processo de soldagem. A área de aplicação mais comum para o monitoramento radiográfico são os encanamentos terrestres e subterrâneos. A análise é realizada direcionando os raios para o tubo usando o equipamento de detecção de falhas. Quando aplicado a serviços públicos subterrâneos, este método de exploração é vantajoso na medida em que não requer a abertura de canais com terraplanagem.
Vale ressaltar as situações em que o uso do controle radiográfico é ineficaz ou não é permitido, devido a limitações técnicas e estruturais:
- Vários tipos de inclusões e descontinuidades, cujo tamanho na direção da transiluminação é menor que a duplicação da sensibilidade do controle.
- Inclusões e descontinuidades próximas a cantos agudos, diferenças ou partes de terceiros fornecidas tecnologicamente. Nas imagens radiográficas, a coincidência de defeitos e elementos estruturais não permitirá determinar com precisão as características da estrutura interna.
- Rachaduras e falta de fusão, em que o avião não coincide com as linhas de transmissão. Neste caso, uma combinação de varredura radiográfica com elementos de teste destrutivos pode ser usada.
Tipos de dispositivos radiométricos usados

Até o momento, os seguintes tipos de equipamentos para monitoramento radiográfico são usados ativamente:
- Dispositivos com frequência constante de radiação gama com intensidade fixa. Desvios nas freqüências causam defeitos no produto, o que é refletido nos radiogramas. Os modelos mais recentes de tais dispositivos são fornecidos com programas que determinam com precisão o espectro vibracional.
- Equipamento de raio X com suporte para flutuações de alta frequência, aleatório no tempo. O grau de flutuação, dependendo da intensidade da radiação, pode exceder 0,5-1%.
- Dispositivos para inspeção radiográfica de juntas soldadas, cuja estabilidade de radiação gama excede 0,5%. Neste caso, a amplitude de oscilação está dentro de 0,1 Hz. Esse equipamento é ideal para escaneamento fino de defeitos de pequeno volume, mas é inadequado para uso na análise de falhas profundas em grandes áreas.
Em termos de controles, quase todos os dispositivos suportam ferramentas automatizadas com a capacidade de ajustar programaticamente os dados recebidos ao gerar radiogramas.
Preparação para inspeção radiográfica

Antes da digitalização, atenção especial é dada à condição do produto e diretamente à solda. O operador inspeciona a peça para identificar defeitos externos, remove as impurezas e, se necessário, marca as áreas. Grandes áreas para digitalização são marcadas por zonas e numeradas sem falhas. Além disso, os padrões com marcação de sensibilidade são definidos em áreas controladas. Por exemplo, os padrões de ranhura devem ser colocados a 5 mm da linha de costura com uma direção transversal. Para obter o resultado mais confiável ao controlar a qualidade das juntas soldadas, podem ser usados cartões de estudos anteriores. Eles são preparados com antecedência e inseridos no sistema de radiograma do equipamento antes da digitalização. Imagens de novas imagens serão formadas com ênfase nos dados anteriores. O software também direciona a digitalização gráfica para explicar os defeitos existentes, fornecendo uma camada separada de informações sobre o grau de progresso das mesmas descontinuidades, rachaduras e falta de fusão.
Determinação de parâmetros de controle
Após a preparação do produto, as características ótimas de seu exame pelo equipamento de varredura são selecionadas. Um dos parâmetros importantes será a distância da fonte de radiação gama à superfície da área alvo, bem como o número e o tamanho das áreas controladas. De acordo com o GOST, as juntas soldadas são escaneadas por equipamentos radiográficos sob as seguintes restrições:
- O aumento no tamanho dos defeitos estruturais localizados ao lado do aparelho da fonte de radiação não deve ser maior do que o coeficiente de 1,25.
- O ângulo entre o normal para o filme fotográfico e a direção da radiação gama não deve exceder 45 ° quando examinado dentro de uma área controlada.
- A desfocagem dos defeitos de imagem ao colocar o filme para fotos próximas à solda não deve ser superior a metade do grau de sensibilidade estabelecido.
- O comprimento das imagens durante a inspeção radiográfica das juntas soldadas deve capturar imagens das seções adjacentes de acordo com a marcação.Se o comprimento da área controlada estiver dentro de 100 mm, então a sobreposição é de pelo menos 0,2 do comprimento total da parcela, e se for uma distância de mais de 100 mm, então a empunhadura deve ser de pelo menos 20 mm.
- No caso de os parâmetros dimensionais dos defeitos não serem determinados, os requisitos para manter a relação entre os diâmetros externo e interno da junta podem ser ignorados.
Esquemas de inspeção radiográfica de juntas soldadas

A eficácia do controle é determinada pelo padrão de transmissão da estrutura do produto. Assim, no processo de varredura das costuras anulares das partes esféricas e cilíndricas, a transiluminação através da parede do elemento é geralmente usada. Além disso, a fonte de radiação radiográfica está localizada dentro do produto, o que permite fixar com mais precisão o mapa de defeitos. Se o diâmetro da parte oca cilíndrica não exceder 2 m, então a inspeção radiográfica de juntas soldadas com esquemas panorâmicos é usada. Mas é importante ter em mente que a análise zonal seletiva da estrutura interna, neste caso, será impossível.
No processo de varredura de juntas de topo, a direção da transiluminação coincide com o plano da área examinada. Tal esquema é usado no trabalho com nós angulares de penetração de conexões e tubos. O ângulo entre a radiação e o plano de junção não deve ser superior a 45 °. Além das configurações padrão, outras direções de transmissão de defeitos também são usadas.
Ao escolher um esquema para o método radiográfico para controle de juntas soldadas, a distância da superfície de análise alvo ao filme do aparelho (não mais de 150 mm) e a exposição de um ângulo de 45 graus na direção da radiação são levadas em conta. Táticas de imagem corretamente selecionadas fornecerão um mapa informativo e preciso com defeitos no produto problemático.
Decodificando imagens radiográficas

A visualização de imagens é organizada em uma sala escura depois que elas secaram usando iluminadores-negatoscópios, que permitem ajustar o brilho e os parâmetros do campo iluminado. Neste caso, requisitos especiais são colocados na qualidade dos materiais:
- Sem riscos, manchas, danos e contaminação na superfície da camada de emulsão. Qualquer coisa que torne difícil a decodificação não deve estar na foto.
- Além dos contornos de defeitos, marcas, marcas e linhas estruturais de contorno, se houver, devem ser refletidas.
- A densidade óptica da placa gráfica gerada durante o controle de qualidade das juntas soldadas na área próxima à junção deve ser pelo menos 1,5.
O processamento de imagens também pode ser realizado em equipamentos de computador de varredura com a geração de modelos de defeitos. Nesse caso, a precisão de determinar a localização e o tamanho do dano na estrutura aumenta.
Separação dos tipos de juntas soldadas de acordo com os resultados do controle
De acordo com os resultados dos dados nas imagens, cada costura é atribuída a uma determinada classe, dependendo do tamanho do defeito. De acordo com os requisitos regulamentares, a classificação é baseada no tamanho dos poros, bem como nas inclusões de óxidos, escórias e tungstênio. Por exemplo, com uma espessura de produto de até 3 mm, é suposto ser dividido em tipos de juntas soldadas, dependendo do comprimento total do defeito - de 3 a 10 mm. Se estamos falando de peças com uma espessura de 200-400 mm, então a faixa de classificação para o mesmo parâmetro irá variar de 10 a 90 mm. Novamente, se o comprimento do radiograma for inferior a 100 mm, os dados calculados sobre o tamanho das inclusões e poros individuais serão reduzidos proporcionalmente ao tamanho da imagem. Além disso, o comprimento dos aglomerados de acordo com os requisitos não deve exceder 1,5 em relação aos comprimentos máximos permitidos para poros individuais e descontinuidades.

Depois de processar os materiais de controle radiográfico, é elaborado um ato especial, que indica os dados sobre o produto e os defeitos que ele contém.Em primeiro lugar, as características da peça ou estrutura são descritas com a indicação de padrões previamente designados e áreas marcadas. A inspeção radiográfica de juntas soldadas pode incluir dados de capacidade, espessura do produto e outros indicadores técnicos e estruturais. Quanto à informação sobre defeitos, toda a lista de informações obtidas como resultado da decodificação de imagens radiográficas é inserida em colunas especiais.
Precauções de segurança ao realizar a inspeção radiográfica
O maior perigo ao realizar uma varredura radiográfica é causado por gases liberados pela radiação gama. Para começar, vale ressaltar a importância das condições de controle que devem atender aos requisitos para o uso de fontes radioativas. O equipamento elétrico utilizado deve estar em boas condições e, se possível, testado imediatamente antes da análise da junta soldada. A radiografia industrial está sujeita a maiores exigências em termos de garantia de segurança elétrica. Isso se aplica a situações de uso de dispositivos estacionários poderosos conectados a redes de energia trifásicas. Sem falhas, os meios de estabilização de tensão e as unidades de proteção contra curto-circuito são introduzidos na infraestrutura.
Prós e contras do monitoramento radiográfico
A radiografia oferece possibilidades bastante amplas de detecção de falhas de solda, permitindo com alta precisão e praticidade a análise das menores falhas na estrutura das estruturas metálicas. As imagens em radiografias são o mais próximas possível da óptica, para que possam ser analisadas não apenas por detectores de falhas, mas também pelos próprios soldadores. Para interpretar os resultados, são emitidos atlas especiais com classificações, de acordo com os quais você pode facilmente avaliar rapidamente os defeitos. Quanto às desvantagens da inspeção radiográfica das juntas soldadas, elas incluem sensibilidade à detecção de descontinuidades planares e baixa confiabilidade ao escanear imperfeições e trincas. Para isso, podemos adicionar a presença de radiação e altos custos financeiros associados ao uso de equipamentos sofisticados em quase todos os estágios de controle.
Conclusão
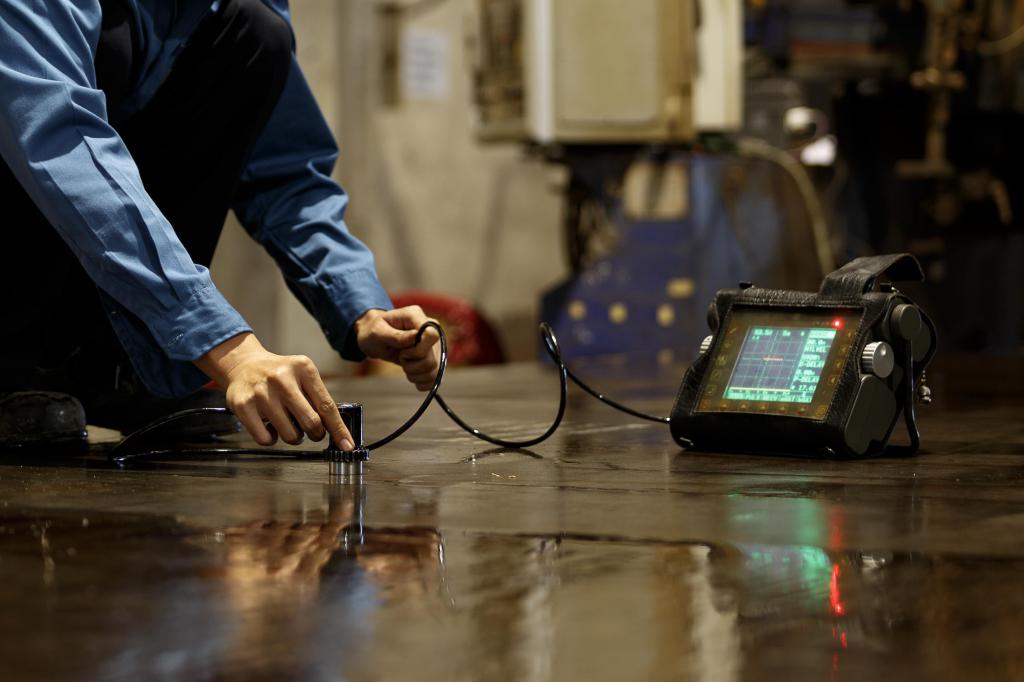
No momento, a radiografia é, embora não seja a mais atraente em termos de vantagens operacionais, mas uma maneira muito conveniente e eficaz de testes não destrutivos de soldas. Basta dizer que, no setor de energia, o controle radiográfico de juntas soldadas de dutos leva cerca de 30% de todos os casos de análise de linhas troncais para a detecção de defeitos. A competição mais próxima desse método é o teste ultrassônico. No entanto, fatores como a necessidade de atualização tecnológica das empresas com a substituição de equipamentos caros e a limitada capacidade de escaneamento do ultrassom ainda impedem a completa exclusão da radiografia. Portanto, em algumas áreas, o monitoramento radiográfico continua sendo indispensável.